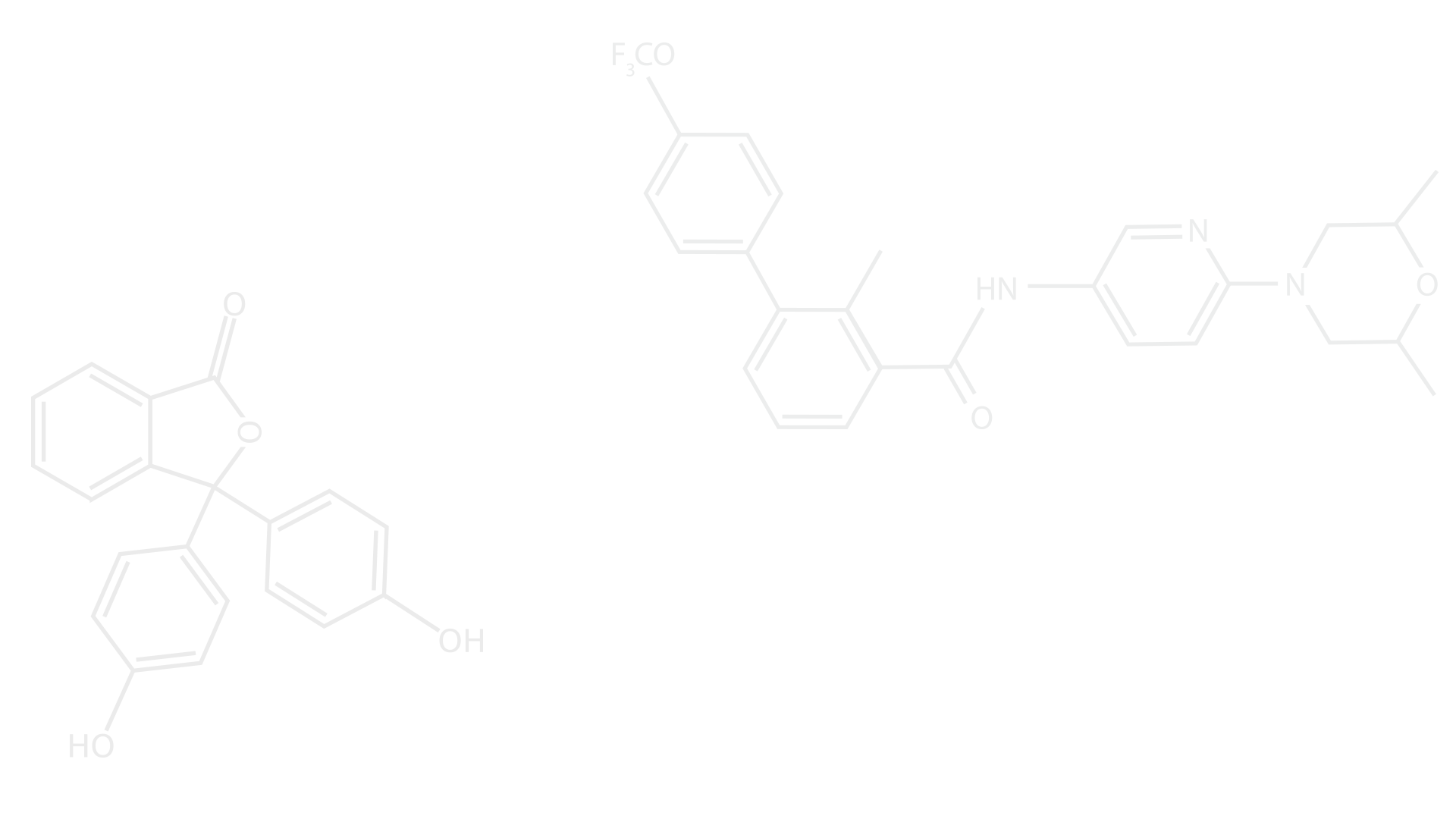
QUALITY ENGINEERING CO-OP
DePuy Synthes Orthopaedics - Warsaw, IN
Supervisor - Joseph Perry

EMPLOYER - DePuy Synthes Orthopaedics
Each company that comprises DePuy Synthes has a celebrated history and has evolved to meet the ever changing needs of the orthopedic and neurological marketplace. In 1895, Revera DePuy founded DePuy Manufacturing in Warsaw, Indiana, on the premise of a fibre splint to replace the wooden barrel staves used then to set fractures; thus establishing the first commercial orthopedic manufacturer in the world. By 1975, DePuy had relocated to its present location at 700 Orthopaedic Dr., Warsaw, Indiana. In 1908, DePuy Orthopaedics began offering the unrivalled method of metal sintering, Provost® Porous Coating, enhancing the tissue in-growth of DePuy systems. This sintering process has the longest clinical history of any porous surface. In 1996, DePuy acquired the former Orthopedic Technology, Inc., which expanded its sports medicine business to include arthroscopic instruments, tissue fixation devices, braces, ankle supports, and soft goods. During this time DePuy, Inc. changed its name to DePuy Orthopaedics, Inc. and the P.F.C. Sigma® Total Knee System was launched; designed to provide the surgeon with surgical solutions for a variety of clinical indications. DePuy Orthopaedics launched the Pinnacle® Acetabular Cup System in 2001, providing surgeons with the options to choose a polyethylene or metal insert for use with the same outer titanium cup that replaces the socket of the natural hip. Finally, in 2011, Johnson & Johnson and Synthes merged to create the world’s most comprehensive portfolio of orthopedic products and services for joint reconstruction, trauma, spine, sports medicine, and cranio-maxillofacial therapies. The DePuy Synthes Companies are also a global leader in neurological solutions, with products and services for neurosurgery, neurovascular, spine, and cranio-maxillofacial therapies.
Johnson & Johnson
The Values, Management Approach, and Company Structure of DePuy Synthes Orthopaedics are greatly defined by those of the overarching Johnson & Johnson Enterprise Policies. The Credo not only acts as a moral compass, but also as recipe for business success, challenging all employees to put the needs and wellbeing of the people served first.
PROCESS QUALITY ENGINEERING CO-OP
Rotation 1 - Spring 2014
CONTINUOUS IMPROVEMENT QUALITY ENGINEERING CO-OP
Rotation 2 - Fall 2014
QUALITY ENGINEERING CO-OP SCHEDULED
Rotation 3 - Summer 2015
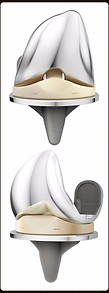
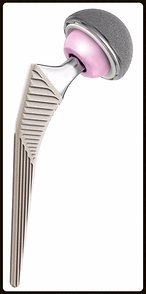

ON JANUARY 6TH, 2014, I BEGAN MY FIRST CO-OP WORK SESSION AS A PROCESS QUALITY ENGINEER FOR DEPUY SYNTHES ORTHOPAEDICS IN WARSAW, IN. UNDER THE SUPERVISION OF THE PROCESS QUALITY ENGINEERING TEAM LEAD, JOSEPH PERRY, I BEGAN MY TRAINING ON THE VARIOUS QUALITY POLICIES, MANUFACTURING PROCEDURES, COMPUTER PROGRAMS, AND COMPLIANCE POLICIES ASSOCIATED WITH DEPUY SYNTHES ORTHOPAEDIC’S PROCESS QUALITY ENGINEERING DEPARTMENT. THE STEEP LEARNING CURVE WAS ALLEVIATED SOMEWHAT BY THE COLLABORATIVE WORK WITH OTHER QUALITY ENGINEERS, QUALITY TECHNICIANS, AND PREVIOUS CO-OPS. THIS SESSION I LEARNED A NEWLY IMPLEMENTED DOCUMENT CONTROL COMPUTER PROGRAM, AND ASSISTED THE QUALITY ENGINEERS CONTROL THE DIFFERENT TYPES OF DOCUMENTS USED AT DEPUY’S WARSAW PLANT. AS I GAINED CONFIDENCE AND EXPERIENCE, I SUPPORTED THE QUALITY ENGINEERS ON VARIOUS PROJECTS RANGING FROM NEW PRODUCT LAUNCHES TO ROUTINE VALUE STREAM METRIC SURVEILLANCE. TOWARDS THE END OF THE SESSION I WAS GIVEN THE PRIVILEGE OF DESIGNING MY OWN PROCESS, WORKING IT THROUGH THOUGHT CONCEPTION, PROBLEM SOLVING, ITERATION, APPROVAL, AND IMPLEMENTATION.
ON SEPTEMBER 10TH, 2014, I RETURNED TO MY SECOND CO-OP WORK SESSION AS A CONTINUOUS IMPROVEMENT QUALITY ENGINEER FOR DEPUY SYNTHES ORTHOPAEDICS IN WARSAW, IN. CONTINUING UNDER THE SUPERVISION OF JOSEPH PERRY I COMPLETED THE REVISED TRAINING ON THE VARIOUS QUALITY POLICIES, MANUFACTURING PROCEDURES, COMPUTER PROGRAMS, AND COMPLIANCE POLICIES ASSOCIATED WITH DEPUY SYNTHES ORTHOPAEDIC’S CONTINUOUS IMPROVEMENT QUALITY ENGINEERING DEPARTMENT. BECAUSE ONLY A FEW ASPECTS OF THE DEPARTMENT, INCLUDING THE JOB TITLES HAD CHANGED, I RETURNED QUICKLY TO MY ROUTINE DUTIES AND RESPONSIBILITIES AS WELL AS ACCEPTING ROLES ON EXISTING PROJECTS. THIS SESSION, I IMPLEMENTED THE SKILLS I LEARNED FROM LAST SESSION ON NEW PROJECTS. I TOOK THE OPPORTUNITY TO ACT WITH THE AUTHORITY OF A QUALITY ENGINEER, COMPLETING MAJOR PROJECTS THAT INCLUDE MEASUREMENT SYSTEMS ANALYSES IN RESPONSE TO NON-CONFORMANCES AND INSTALLING, PROGRAMING, AND VERIFYING A NEW VISUAL OPTICAL COMPARATOR MACHINE FOR PART INSPECTION.
ON MAY 11TH, 2015, AS A JUNIOR IN THE WELDON SCHOOL OF BIOMEDICAL ENGINEERING AT PURDUE UNIVERSITY, I RETURNED FOR MY FINAL CO-OP WORK SESSION AS A CONTINUOUS IMPROVEMENT QUALITY ENGINEER FOR DEPUY SYNTHES ORTHOPAEDICS IN WARSAW, IN. THE EMPLOYER COORDINATOR ON BEHALF OF DEPUY PRODUCTS, INC. IS VIKKI BERGER, THE SENIOR UNIVERSITY RECRUITER. MY SUPERVISOR FOR THIS SESSION IS JOSEPH PERRY, THE CONTINUOUS IMPROVEMENT QUALITY ENGINEERING TEAM LEAD.
AS A CONTINUOUS IMPROVEMENT (CI) QUALITY ENGINEER FOR DEPUY SYNTHES ORTHOPAEDICS, I COMPLETED THE REVISED TRAINING ON THE VARIOUS QUALITY POLICIES, MANUFACTURING PROCEDURES, COMPUTER PROGRAMS, AND COMPLIANCE POLICIES ASSOCIATED WITH DEPUY SYNTHES ORTHOPAEDIC’S CI QUALITY ENGINEERING DEPARTMENT. BECAUSE ONLY A FEW ASPECTS OF THE DEPARTMENT HAD CHANGED, I RETURNED QUICKLY TO MY ROUTINE DUTIES AND RESPONSIBILITIES AS WELL AS ACCEPTING ROLES ON EXISTING PROJECTS. THIS SESSION, I GAINED GROUND AS A MORE INDEPENDENT QUALITY ENGINEER, WHERE THE MANAGERS TRUSTED ME, AND WHILE I DID NOT HAVE APPROVER STATUS, THEY READILY ACCEPTED MY WORK AS HIGH QUALITY AND ACCEPTABLE. I TOOK THE OPPORTUNITY TO ACT WITH THE AUTHORITY OF A FULLY-FLEDGED QUALITY ENGINEER, COMPLETING MAJOR PROJECTS THAT INCLUDE MEASUREMENT SYSTEMS ANALYSES IN RESPONSE TO NON-CONFORMANCES AND INSTALLING, PROGRAMING, AND VALIDATING A NEW OPTICAL VISION SYSTEM FOR PART INSPECTION DESIGNED FOR USE IN PACKAGING TO CONFIRM THAT THE PACKS ARE ORIENTED CORRECTLY WITH THE CORRECT PRODUCT. I ATTENDED TRAINING SESSIONS AND BECAME A SUBJECT MATTER EXPERT ON THE USE AND INSTALLATION OF AIR GAGE EQUIPMENT FOR MEASURING TAPERS AND DIAMETERS. FINALLY, I WORKED ON THE DEVELOPMENT OF RISK ASSESSMENT DOCUMENTATION INCLUDING PROCESS FAILURE MODES AND EFFECTS ANALYSES, RISK MANAGEMENT REPORTS, AND MANUFACTURING CONTROL PLANS.