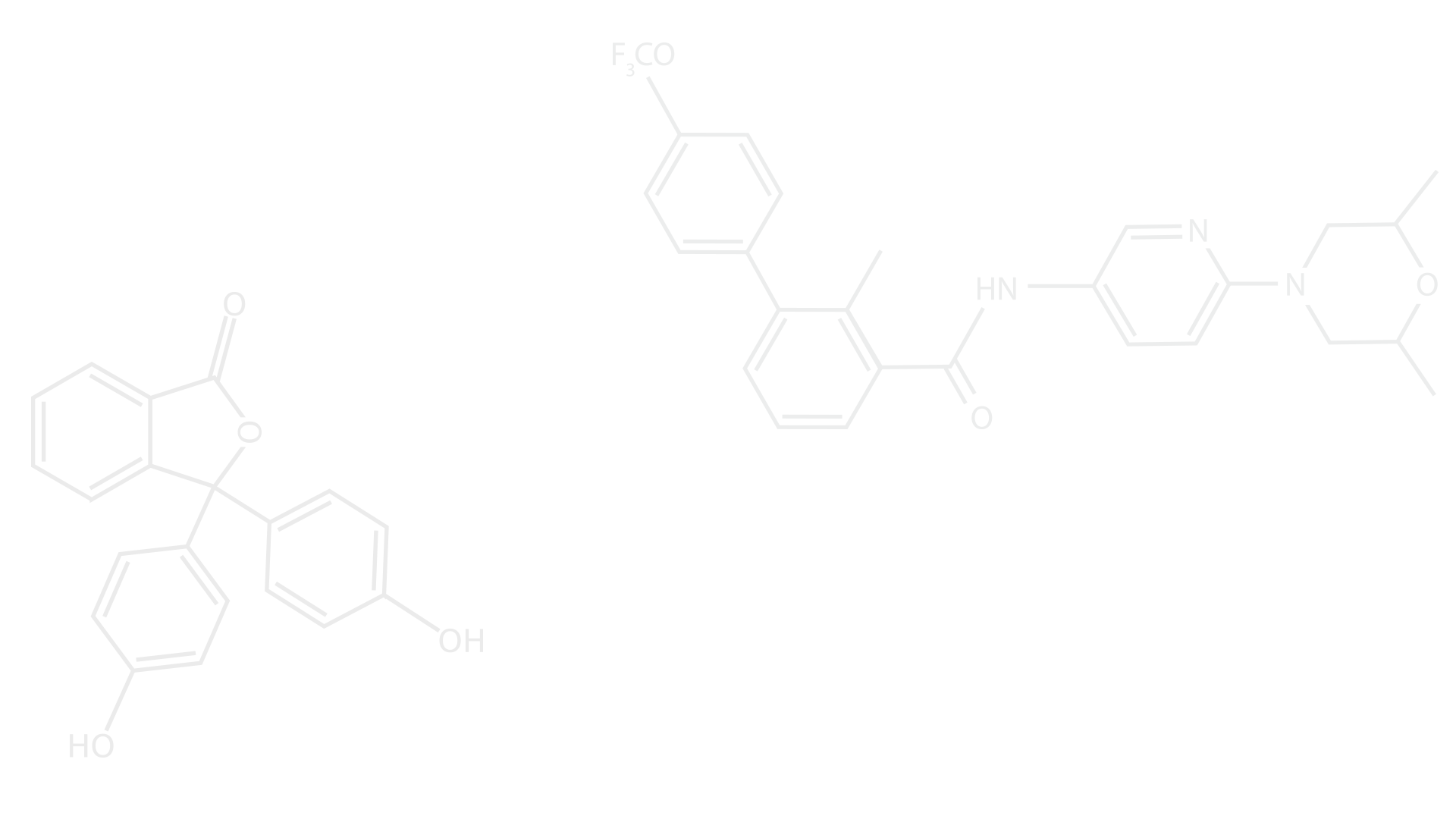
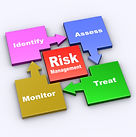
PFMEA & RMR
GAP ASSESSMENT

SUI/SOLO
VISION SYSTEM
VALIDATION
As I progressed into my final work session, I was given a project in related to a new product launch. The Attune SOLO or Single Use Instrument packs were about to be launched in Warsaw, and it was our job as Quality Engineers to work with a supplier and develop a vision system that will verify the operators work before the package is sealed. Attune is DePuy Synthes’ new Knee product launch and has been launched previously as a continuous use product. This means that the instrumentation and trial pieces that help the surgeon prepare the patient for the implant and verify the correct implant size and orientation, can be used multiple times and cleaned and sterilized in between uses. The SOLO packs are single use packs and eliminate the cleaning and sterilization steps for the consumers. So instead of being packed in large trays that are used multiple times, these are packaged in blister packs and trays that can be discarded with the instruments and the trials after surgery. In order for this product to be profitable, DePuy must increase the amount of product produced, so they are creating a new clean room environment where operators will package upwards of 250 SOLO packs per lot. Based on the sheer volume of product and the number of pieces in each tray, there is much room for human error where a piece may be packaged incorrectly in a pack. To combat this potential risk, we designed a vision system to check the operators work, confirming the packs have the correct pieces in the correct orientation. In order for this system to be used, we must validate that it is working properly and prevents bad packages from being passed with a specific degree of confidence.
My job was to develop a test script as part of the Installation Qualification (IQ) study to validate these vision systems, verify the programing functionality and proof of concept, and run the test script through to completion. I worked with another engineer to determine the appropriate test function and script steps to evaluate the effectiveness of these systems. This included, in addition to the basic software tests, changing the orientation of the individual pieces, removing pieces from the pack, adding additional pieces to the pack, and replacing them with incorrectly sized pieces. All the different tests made the IQ rather long and validation took about four days per machine. Initial testing was used to confirm the proof of concept and identify software issues, and the validation IQ acts as the final test of the machine, catching any issues that were not previously identified. After the system is validated, the engineer will write a report from the results of the test script and confirm that the system is validated by having it approved in ADAPTIV by other engineers and managers.
This project and others gave me great insight into more of the specialized challenges Quality Engineers face at DePuy with respect to new product launches. I saw the scheduling plan, regulatory compliance, and other formal restrictions that affect all of the steps along the way to a successful launch. Even something as simple as a camera used to confirm correct orientation of pieces in a pack takes careful planning and engineering best practice to ensure the safety of the consumer and employees in addition to verifying the functionality of the inspection method. This project has helped me realize the overall goal is to deliver a system that produces a safe and high quality product to the customer and the patient in a timely and robust manner.
In alignment with Joe’s FPX project related to the revision and robustness of production Risk Management and Process Failure Modes and Effects Analysis for the Warsaw Plant, I created and maintained a database of all the associated Risk Management documents in two isolated controlled environments in attempt to analysis the gaps in our production and processes with respect to risk management. This analysis incorporated Planners, Manufacturing Engineers, and Quality Engineers to determine the relevance of the active documents in our controlled Project Lifecycle Management system (ADAPTIV), as well the legacy L Drive. From this analysis, we have identified areas of potential improvement in addition to confirming our risk management compliance with an upcoming rollout of new J&J Standards. This gap assessment was based off of the active product made in this facility, and the planners helped me determine the coverage of our risk management documents. During this process, I learned the importance and meaning behind the development of robust Risk Management documents from not only a compliance standpoint, but also a business and patient risk analysis. If these documents are completed effectively and used in correlation with a Manufacturing Control Plan, risk can be well mitigated and captured to protect the consumer and the patient as well as the business.
I was also involved with another Quality Engineer’s FPX project in the development and implementation of Manufacturing Control Plans. With the coming updates to the J&J MD Standards, DePuy must implement Manufacturing Control Plans and monitor them accordingly. As Quality Engineers, we own these documents and are responsible for its accuracy with respect to the actual process, but developing these plans involves that direct input from manufacturing engineers, operators and management. These plans essentially go line-by-line through the entire manufacturing process of a specific product family and establish the major processes, machines, critical to quality points (CTQs), inputs, outputs, acceptance criteria document references, critical control points (CCPs), reaction triggers and plans, and control justification document references. As a quality engineer, a Value Stream quality engineer specifically, I should be able to identify the major process steps and critical to quality points for the product families that I own. From this information, I was able to understand and draft five different Manufacturing Control Plans. These plans were for many different orthopedic products including Revision Knee systems, Poly Hip Liner Bearings, Titanium Hip Stems, and Titanium Acetabular Hip Cups. After completing the draft, we hold a meeting to determine the CCPs and the reaction plans, so these meetings include the many individuals to create a sense of ownership of the process and the CCPs. CCPs are a new concept to maintain a sense of importance for operations that may create a Critical Defect or a defect that will lead to patient harm or surgical delay. In addition to these plans, CCP flags will be created to show the operator what harms may result from a passed defect at the operation.
The implementation of Manufacturing Control Plans is complex and difficult to develop, but after it is established, it will be an important document for all levels of the plant; from an operator who need to know how to react to a defect, to a manager who need to understand the relationship of a risk assessment to the manufacturing process. In my attempt to compile the vast about of information necessary for a Manufacturing Control Plan, I gained great insight into our inspection and process controls as a Quality Engineer as well as the big picture related to orthopedic manufacturing process creation.
An additional duty includes a bi-weekly meeting with my supervisor, discussing the top five items that I am currently working on. This includes discussing the projects that have been allocated to me as well as the projects I am assisting the other quality engineers on and determining a percentage of time to devote to each project. This is also a time for me to ask questions about the industry, quality systems, employment opportunities, and other professional topics. My supervisor’s insight into the industry has provided me with a good understanding of the field, what I can expect from a career, and what steps I need to take academically and personally to secure a position in the field.
The Value Stream Quality Engineers occasionally include me on some of their projects including Value Stream Meetings. The difference between CI Quality Engineers and Value Stream Quality Engineers is basically long term versus short term responses to quality functions. This can also be described as the difference between New Product Introduction and Base Business Support groups respectfully. Value Stream Quality Engineers focus on keeping production up from a quality perspective and generate trend data to monitor our processes. Alternatively, Continuous Improvement Quality Engineers focus on bringing in new technology, validating and verifying processes, launching new products, and responding to major quality issues alongside the Value Stream Quality Engineers.
Finally, before the end of each rotation, I am responsible for giving a short presentation on my involvement in these projects. Additionally, I report what I have learned, what I have enjoyed, and what I would like to improve upon from this work session and this entire co-op experience as a whole.

Manufacturing Control Plan Implementation

ADDITIONAL
DUTIES &
RESPONSIBILITIES
CONTINUOUS IMPROVEMENT QUALITY
ENGINEERING CO-OP
DePuy Synthes Orthopaedics - Rotation 3
Summer 2015 - May 11th to August 14th
REFLECTION
SIMILARLY TO MY PREVIOUS ROTATIONS, I HAVE UNDOUBTEDLY GAINED TREMENDOUS INSIGHT INTO ENGINEERING APPLICATIONS WITH REGARD TO QUALITY SYSTEMS AND ORTHOPEDICS. QUALITY ENGINEERING HAS TAUGHT ME THE REALITY OF ENGINEERING IN THE CORPORATE WORLD, WHERE SAFETY, COMPLIANCE, AND CONTROL MUST BE PRIORITIZED IN PRODUCTION OF IMPLANTS WHICH ARE DESTINED TO INTERACT, OFTENTIMES DIRECTLY, WITH THE HUMAN BODY. WORKING IN A MANUFACTURING ENVIRONMENT HAS GIVEN ME AN OUTLOOK INTO THE BREADTH OF THE ORTHOPEDIC WORLD, LEARNING THE DIFFERENT PRODUCTS, THEIR APPLICATIONS, THE MANUFACTURING PROCESS, LIMITATIONS BETWEEN DESIGN AND MANUFACTURING, LOGISTICS, FINANCIAL IMPACTS, AND EVEN EXPOSURE TO RESEARCH AND DEVELOPMENT. THIS EXPERIENCE THROUGH MY FINAL SESSION EXCEEDED MY EXPECTATIONS OF WHAT I WOULD BE DOING AND LEARNING AS JUST A JUNIOR CO-OP AT DEPUY SYNTHES ORTHOPAEDICS AND HAS PROVIDED ME A WINDOW TO GLIMPSE THE DIFFERENT CAREER PATHS NOW AVAILABLE FOR MY PURSUIT.
PROJECTS
During this work session, like the last, some of my responsibility lay in the controlling of documents for the quality engineers. This Project Lifecycle Management system, ADAPTIV, controls what documents the company uses when they make orthopedic implants and other products. The documents govern the products, processes, equipment, gages, calibration, supplier outsourcing, packaging, and many other aspects of the company as a whole. I am still a strong asset for my department in this regard, teaching many of the engineers and the new hires how to efficiently control documents in this system.

ADAPTIV
In addition to the major projects that I worked on, I was privileged to learn the major software and hardware applications for Air Gaging. Air gaging is an inspection method that uses air jets to measure the relative back pressure created by putting a taper into a spindle. The air pressure is then converted into an electronic reading by a converter. A computer then takes the raw data, and then, through geometry calculations and calibration configurations, displays meaningful results to the operator. Air gages are designed to read raw data related to the diameter and taper angle of a taper, but calculations can be used to measure half angle and other functionality. Calibration, error checking, diagnostics, and maintenance of these systems can be challenging, but I learned a great deal about them when a Jenoptik Hommel-Etamic representative held a training program for our engineers. He went through the individual gages for each engineer’s product families, but I was able to stay for each session with each corresponding engineer. During that time I gleaned more information regarding the calibration and programing of the specific machines. This information included the more difficult configurations including mastering and offset and coefficient management. This opportunity reflects the interesting circumstance where the co-op can lead in a topic that is not product specific or value stream specific as I did similarly in my last two rotations related to the pin gage project.

AIR GUAGE
SUBJECT MATTER EXPERT

FPX - EPICS
INTEGRATION
Flawless Project Execution (FPX), as I have referenced above, is a project leadership and management methodology used with J&J Companies as an industry standard means of project execution. Fortunately, during my second rotation, I attended the training workshop for this methodology and was captivated by its effectiveness and ease of application. I took what I had learned from this workshop and applied it towards the Abōd EPICS team at Purdue during the spring of 2015. This toolset gave me that advantage I needed to lead a group of 14 aspiring Engineering Students from a dysfunctional group of individuals into a team driven to help create a design for disaster relief housing. My success caught the attention of the EPICS coordinators and my professor, and this summer I focused on the development of a formal relationship between J&J and Purdue with the hope of creating an FPX workshop focused on molding new Project Leaders and Managers from academia. This process broke me out of my comfort zone as I introduced myself to the FPX Director from J&J Headquarters. J&J and Purdue are now primed to introduce a pilot FPX program in the fall of 2015, and I learned that I can reach out, make new connections, and succeed as an aspiring engineering leader.
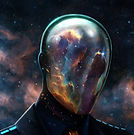
FUTURE PLANS
FINAL REFLECTION
While the majority of my projects this work session will be complete, there are a few that I am leaving incomplete. This means that I am preparing a transition plan for the next co-op in order to appropriately assist the engineers that I am working with on these projects. As I predicted last rotation, I completed my goal to open a career opportunity path and establish connections within the company that may lead to employment after graduation. While I will be unavailable for employment until my graduation in May of 2017, I have built a network with DePuy and parts of J&J in order to maintain contact and review the availability for employment opportunities in the coming years. I would like to return to the CI Quality Department if an opening is available, but I am open to other positions throughout J&J.