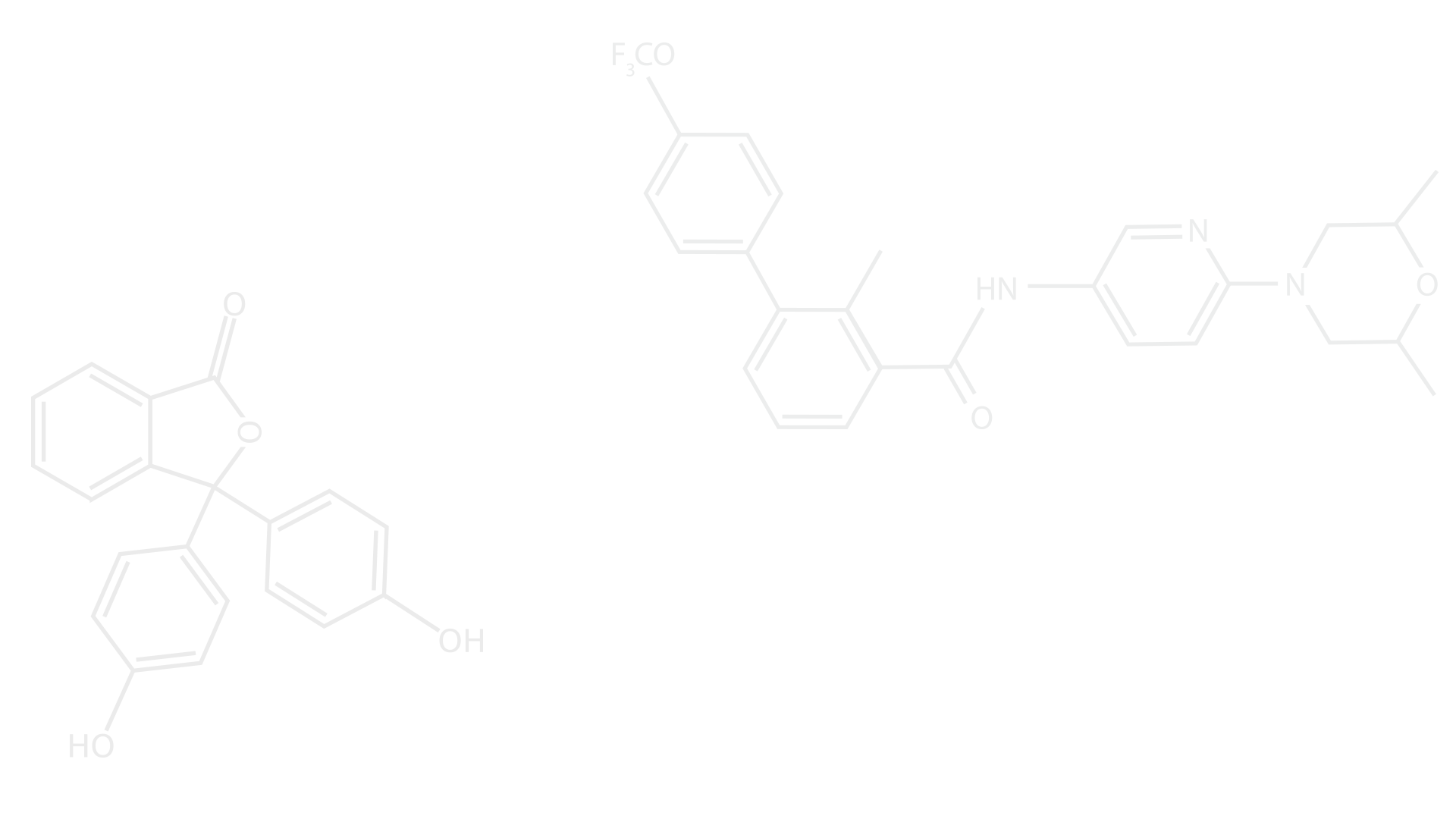
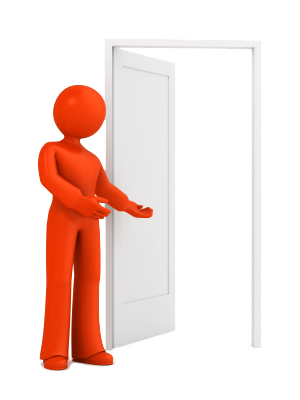
NEW
HIRE
TRAINING
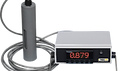
ELECTRONIC HYDROMETER IMPLEMENTATION
One of my major projects was in response to a corrective action item. The corrective action requires a response an input on the passivation line being out of specification. Namely, the concentration of nitric acid was outside of the validated limits for operation of the passivation line. Previously, nitric acid concentration was monitored by operators manually measuring the specific gravity of the fluid using a hydrometer. Because the operators are only required to check the concentration of the nitric acid at the beginning of each shift, there was enough time for the specific gravity to rise above the validated limit. In response to this nonconformance, all batches of product that were passivized during that shift must be run through the passivation line again after the concentration of nitric acid was normalized. In order to correct this process to affect less product, the process engineers decided that electronic hydrometers should be implemented to dynamically read the specific gravity of the nitric acid. Additionally, the dynamic reading will automatically shut off the passivation line if the specific gravity goes outside the validated range. As part of implementing this change, quality operations must validate the use of these new hydrometers so that it is known that the hydrometers are operating correctly with a specific degree of confidence.
My job was to conduct the study to validate these hydrometers, create a calibration procedure, and ensure these gages are correctly monitored through the gage management system. I worked with another engineer to determine the appropriate type of study to evaluate the effectiveness of these gages. Because the gages will not be directly used by the operators, reproducibility between operators is not a concern and a full Gage Reproducibility and Repeatability is not necessary. It is more appropriate to analyze the linearity, bias, and repeatability of the gage to determine if the hydrometers selected are an appropriate gauging method. I used Minitab statistical software and other resources to familiarize myself with the different Measurement System Analyses I would be using. The method basically tests the accuracy of the hydrometers when used to measure fluids of known specific gravity. From the analysis of the study, I was able to determine the tolerance for these gages and begin to write the calibration procedure.
Calibrating these gages proved to be a difficult task, because they are electronic and must be calibrated to the device that they are used to display the reading. This means that whatever Specific Gravity Standards used to calibrate them must not come into contact with the nitric acid tank. To find the solution to this problem, I collaborated with the Process Engineer and the electronic hydrometer manufacturers. Our solution consisted of calibrating an external display, separate from the passivation line, to an extra electronic hydrometer outside of the plant floor to prevent contamination. Then the extra hydrometer is cleaned thoroughly and brought with the external display to the passivation line. Then they take a reading from the nitric acid tank and compare it to the one installed in the passivation tank. Any discrepancy will be the deviation in the installed hydrometer. The calibration tech can then tell if the unit is within the tolerance I determined in the study, and adjust the display on the passivation line to return the offset to zero.
Finally, I was able to coordinate with the Process Engineer and our electronic installation supplier to install these electronic hydrometers after determining that this is an appropriate gauging method to determine the concentration of the nitric acid in the Passivation tank. The hydrometers will not be able to turn off the passivation line until we have monitored them for a couple weeks. This will also us to monitor how much the concentration changes overtime and look for wear on the gages.
This project and others gave me great insight into more of the technical challenges Quality Engineers face on a long term basis. Time, regulatory compliance, and other formal restrictions affect all of the steps I took along the way to success. Even something as simple as a gage to measure the specific gravity of a fluid takes planning and engineering best practice to ensure the safety of the consumer and employees in addition to verifying the functionality of this gaging method. This project has helped me realize the overall goal is to deliver a system that produces a safe and high quality product to the customer and the patient.
Two times during this work session I was responsible for initiating a new hire into our work environment. I was honored that Joe felt I was qualified to train two new people in our department. The first was a new quality technician, who replaced the person that trained me. I worked to bring her up to speed on many of the tools that I learned during my first rotation. She reports to Joe, but I delegate some work so that she learns the tools through applying them. Some of these responsibilities include familiarizing her to the document control system, ADAPTIV, training her to her routine responsibilities as the quality technician, and familiarizing her to the plant floor and the DePuy Warsaw, IN facility. She will be training the new CI Quality Engineering Co-op in the Spring. The second person I helped bring up to speed was the new Value Stream Quality Engineer responsible for the Final Clean and Pack Value Stream. This individual has very good quality engineering experience so I was mostly responsible for acclimating her to the DePuy Warsaw, IN Facility and the work environment here.
During this work session, like last, some of my responsibility lay in the controlling of documents for the quality engineers. This system, ADAPTIV, controls what documents the company uses when they make orthopedic implants and other products. The documents govern the products, processes, equipment, gages, calibration, supplier outsourcing, packaging, and many other aspects of the company as a whole. I am still a strong asset for my department, teaching many of the engineers and the new hires how to efficiently control documents in this system.
An additional duty includes a weekly meeting with my supervisor, discussing the top five items that I and currently working on. This includes discussing the projects that have been allocated to me as well as the projects I am assisting the other quality engineers on. This is also a time for me to ask questions about the industry, quality systems, employment opportunities, and other professional topics. My supervisor’s insight into industry has provided me with a good understanding of the field, what I can expect from a career, and what steps I need to take academically and personally to secure a position in the field.
Another major project has been the Installation Qualification (IQ) of a new inspection technology that we are implementing in the Warsaw, IN facility. I have been given the task to write the General Use Work Instruction for the quality engineers to program the machine. This also includes working with the manufacturing engineers to create fixtures and with the operators to make gage instructions to run parts on these machines.
The Value Stream Quality Engineers sometimes include me on some of their projects including Value Stream Meetings. The difference between CI Quality Engineers and Value Stream Quality Engineers is basically long term versus short term responses to quality functions. Value Stream Quality Engineers focus on keeping production up from a quality perspective and generate trend data to monitor our processes. Alternatively, Continuous Improvement Quality Engineers focus on bring in new technology, validating and verifying processes, launching new products, and responding to major quality issues alongside the Value Stream Quality Engineers.
Finally, before the end of each rotation, I am responsible for giving a short presentation on my involvement in these projects. Additionally, I report what I have learned, what I have enjoyed, and what I would like to improve upon from this work session.

ADAPTIV

ADDITIONAL
DUTIES & RESPONSIBILITES
CONTINUOUS IMPROVEMENT QUALITY
ENGINEERING CO-OP
DePuy Synthes Orthopaedics - Rotation 2
Fall 2014 - September 10th to December 16th
REFLECTION
SIMILARLY TO MY FIRST ROTATION, I HAVE UNDOUBTEDLY GAINED TREMENDOUS INSIGHT INTO ENGINEERING APPLICATIONS WITH REGARD TO QUALITY SYSTEMS AND ORTHOPEDICS. QUALITY ENGINEERING HAS TAUGHT ME THE REALITY OF ENGINEERING IN THE CORPORATE WORLD, WHERE SAFETY, COMPLIANCE, AND CONTROL MUST BE PRIORITIZED IN PRODUCTION OF IMPLANTS DESTINED TO INTERACT, OFTENTIMES DIRECTLY, WITH THE HUMAN BODY. WORKING IN A MANUFACTURING ENVIRONMENT HAS GIVEN ME AN OUTLOOK INTO THE BREATH OF THE ORTHOPEDIC WORLD, LEARNING THE DIFFERENT PRODUCTS, THEIR APPLICATIONS, THE MANUFACTURING PROCESS, LIMITS BETWEEN DESIGN AND MANUFACTURING, LOGISTICS, FINANCIAL IMPACTS, AND EVEN EXPOSURE TO RESEARCH AND DEVELOPMENT. THIS EXPERIENCE THROUGH MY SECOND SESSION EXCEEDED MY EXPECTATIONS OF WHAT I WOULD BE DOING AND LEARNING AS JUST A SOPHOMORE CO-OP AT DEPUY SYNTHES ORTHOPAEDICS.
PROJECTS
From our weekly individual meetings, Joe presented me with his thoughts for development of the co-op position of the Process Quality Department. His plan parallels the up and coming changes in the department. These changes include splitting the department into two entities. One focused on manufacturing support while the other emphasizes continuous improvement to the quality operations and systems. The co-op role will fall under the continuous improvement category. Kody, the co-op on the alternative rotation schedule, will begin his second rotation summer 2014 and Joe plans to give him a major role in a project under the guidance of a Quality Engineer. Similarly, if the project is not complete by that time, I will take over Kody’s duties when he completes his rotation. The focus of the project is to redesign the Process Validation process. Joe wants the Quality Engineer, with the co-op support, to simplify and fortify the procedure, making it a robust process for any future Process Validations. The procedure is currently complex because Process Validations are often very case specific because they cannot be verified through simple testing like in Process Verification. Joe intends to give the co-ops consecutively more responsibility and designate specific projects or Value Streams to focus our attention. In later rotations I will also be required to plan ahead and report to top three items that I plan to work on or complete during the week in our weekly meetings. This is more similar to what the Quality Engineers are required to do themselves. I am excited to begin to specify with in the Process Quality Department and begin developing more robust quality systems at DePuy Synthes.
