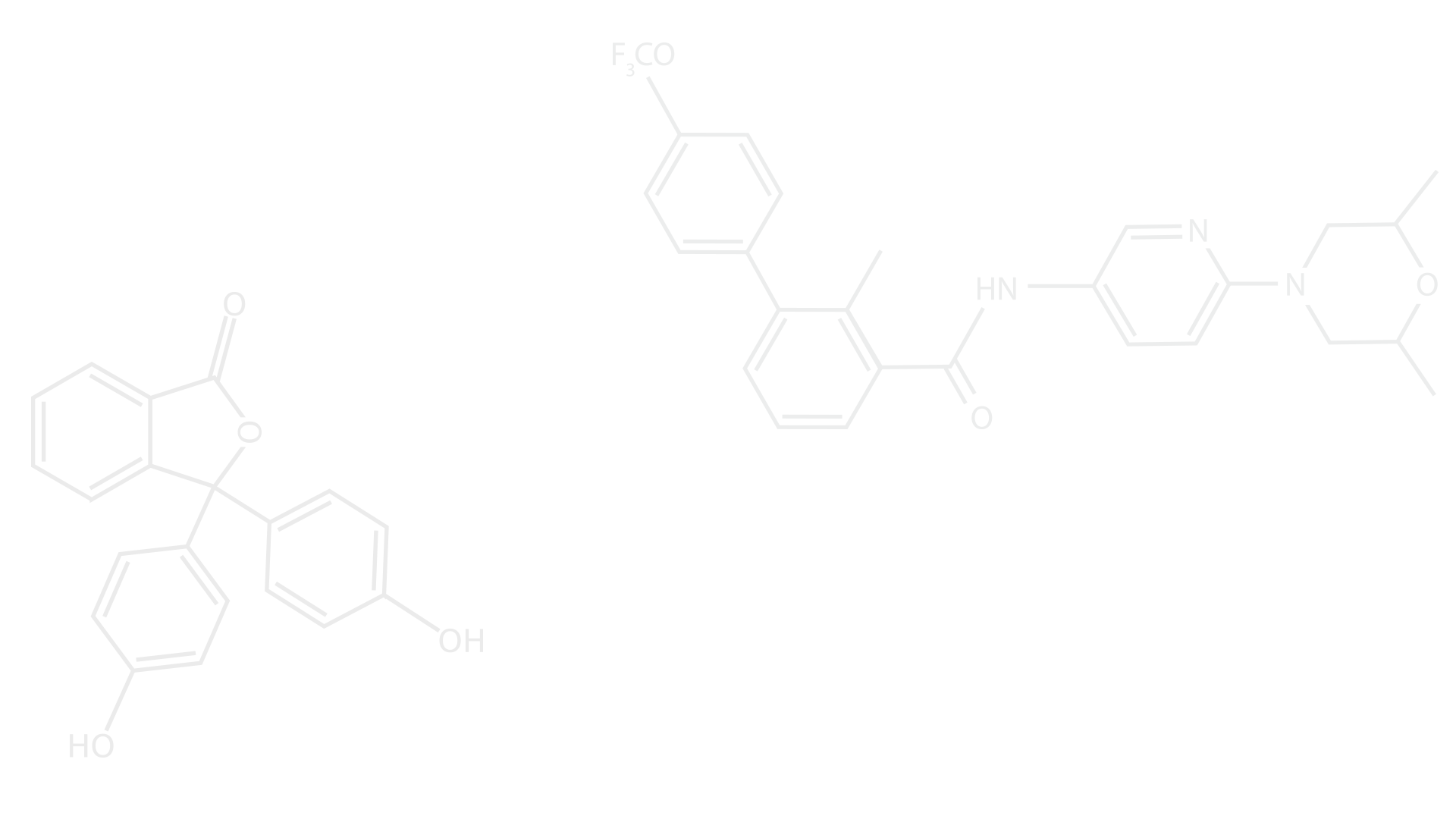

ADAPTIV
PROJECT

PIN GAGE
SET CONTROL
PROJECT
Midway through my first work session, it was discovered that our current system implemented to control the use of individual cylindrical pin gages from large pin gage sets was not providing sufficient traceability and control of where, when, and which pins were being used to gauge products. Unfortunately, this was a plant wide problem, and the way our Quality Engineers are divided up into Value Streams, there was no appropriate engineer that could devote his time to solve this issue. I took this opportunity to take on my own project and help my department. The response to this finding required both a short term and long term fix to the problem.
The short term fix is a temporary solution with the goal of deriving a method of issuing the individual gages from the large set and retaining control. I met with each of the direct users to determine what each actually needed out of this work instruction. Quality needs a form to retain information for record retention pertaining to calibration, the date issued, sizes of pins issued, where they were issued to, who requested them, when they were returned, and the supervisor that oversees the process. From these requirements, I developed the procedure described below.
Operators request specific size pins from the Gage Crib with a pink slip form. The Crib Attendant retains the pink form for the Quality Assurance Supervisors use and issued the Operator the pins requested in a small zip-lock bag with the calibration control label of the large set and the controlled gage label. Additionally the attendant prints out an additional label with the specific sizes issued and puts it on the bag. The Operators, if they request more than one pin only use one pin from the bag at a time, returning them to the bag as they are finished with them. When the Supervisor receives the pink slips, he records the information on the records retention form. When the pin gage set is due for calibration, the form, pink slips, bags, and set are returned to calibration. Calibration calibrates the set, creates new bags with updated labels, and returns the forms and slips to the supervisor. The supervisor then works with Calibration System Management (CSM) to submit a scan of the form for electronic record retention in the Gage Management System under the appropriate gage set. If the set is returned to calibration with missing pins, the supervisor uses the form to identify where the pins were issued to and recover them or make appropriate decisions for missing pins. This form can also be used to identify if the correct pin was used in response to non-conforming parts related to pin gages. I completed the creation of this new process and still follow up with the users to receive feedback and information that is important to the long term fix.
The goal for the long term fix is not as seemingly complex, but requires some time to complete because it means replacing the individual pins issued with permanent gages for each work center. This means that our department has to determine every operation where the pins are called out and remove them from the system and ensuring they are the correct sizes the Operators should be using. For this I cross-referenced our Process Inspection Criteria (PIC) in the Document Control Program (1,500 plus documents) with all the Operations in the Manufacturing Router Program (100,000 plus operations) and discovered that about 300 documents call out the pin gage sets. Then I worked with the appropriate Quality Engineer who is responsible for the PICs and determined the appropriate actions whether that is removing the reference to the set, ordering additional replacement gages, or using an alternative gage. After determining these changes, I requested a quote for the respective gages and ordered the gages from a company supplier. Currently, I and the co-op for the summer rotation are completing the process of entering the new gages within our system to replace the individual pins from the sets. We are on track to complete the long term fix before the three months are over.
This project, and others, gave me great insight into the challenges Quality Engineers face on a daily basis. Time, regulatory, and other formal restrictions affect all of the processes they design, even if they are as simple as identifying where pin gages have been used, and they must be within compliance. Additionally they must meet the needs of all functions involved and derive solutions to any conflicts or problems that arise. They must also realize that their overall goal is to deliver a system that produces a safe and high quality product to the customer and patient.
During this work session, the majority of my responsibility lay in controlling documents for the quality engineers. DePuy switched document control systems from Agile to ADAPTIV just as I began my session. These systems control what documents the company uses when they make orthopaedic implants and other products. The documents govern the products, processes, equipment, gages, calibration, supplier outsourcing, packaging, and many other aspects of the company as a whole. This is a major change to Process Quality because the responsibility to maintain compliance for many of these documents falls to this department.
As a Co-op who has to learn these programs with no previous control program experience, I was able to objectively learn the system. Due to this and an extra week of additional ADAPTIV transition training, I became a strong asset for my department to use to learn and efficiently control documents using a system with a steep learning curve. I was the go-to person for anyone with an ADAPTIV question, and was even able to help the other product development co-ops learn the system when they were lost. Toward the end of the session I focused on teaching the other quality engineers in my department the tips and other useful insight into the program so they can perform their other duties and not focus on fighting with a computer. This also included creating a reference only document that walks through the standard procedure for a change to a controlled document.
An additional duty includes a weekly meeting with my supervisor, discussing the top three items that I worked on during the previous week. This includes topics like major projects I am assisting the Quality Engineers, individual projects, and major control document changes. This is also a time for me to ask questions about the industry and quality systems. My supervisor’s insight into quality systems has provided me with a good understanding of the field, what I can expect from a career, and what steps I need to take academically and personally to secure a position in the field if I feel so inclined to pursue a similar career.
Some of the Quality Engineers included me on projects that include data collection and analysis to develop convincing statistical evidence for different quality operations. These operations include process verifications protocols and reports (PVEs), process validations protocol and reports (PVAs), Installation/Operational/Performance Qualification protocols and reports (IQ/OQ/PQs), gage repeatability and reproducibility reports (GR&Rs), and Process Failure Modes and Effect Analyses (PFMEAs). Many of these tasks include interacting with the operators on the floor and learning about the manufacturing techniques in addition to looking for additional quality issued that can be addressed as continuous improvement.
The Quality Engineers sometimes also included me on Value Stream Meetings. Currently, Value Streams are different parts of the manufacturing floor devoted to developing particular product lines. The current ones are Excel, Summit, Round & Shiny, General, Receiving Inspection, Pinnacle, Poly, and Specials. Each Quality Engineer is responsible for meeting with the supervisors and other representative from one or more of the value streams to review the metrics for that particular value stream. The topics include: Safety, Scrap, Calibration, Non-Conformance, Close Calls, Corrective and Preventive Actions (CAPA), Complaints, Audits, and Hold Ticket. The review of these items gives the Quality Engineering an overview of the status of their Value Stream and alerts them to any major issues or trends that they need to address.
Finally, before I leave each rotation, I am responsible for giving a short presentation on my involvement in projects. Additionally, I report what I have learned this rotation, what I enjoyed about the rotation and work, and what challenges or improvements I need to make for my next rotations.
From our weekly individual meetings, Joe presented me with his thoughts for development of the co-op position of the Process Quality Department. His plan parallels the up and coming changes in the department. These changes include splitting the department into two entities. One focused on manufacturing support while the other emphasizes continuous improvement to the quality operations and systems. The co-op role will fall under the continuous improvement category. Kody, the co-op on the alternative rotation schedule, will begin his second rotation summer 2014 and Joe plans to give him a major role in a project under the guidance of a Quality Engineer. Similarly, if the project is not complete by that time, I will take over Kody’s duties when he completes his rotation. The focus of the project is to redesign the Process Validation process. Joe wants the Quality Engineer, with the co-op support, to simplify and fortify the procedure, making it a robust process for any future Process Validations. The procedure is currently complex because Process Validations are often very case specific because they cannot be verified through simple testing like in Process Verification. Joe intends to give the co-ops consecutively more responsibility and designate specific projects or Value Streams to focus our attention. In later rotations I will also be required to plan ahead and report to top three items that I plan to work on or complete during the week in our weekly meetings. This is more similar to what the Quality Engineers are required to do themselves. I am excited to begin to specify with in the Process Quality Department and begin developing more robust quality systems at DePuy Synthes.

ADDITIONAL
DUTIES &
RESPONSIBILITIES

ROTATION 1
TRANSITION
PROCESS QUALITY ENGINEERING CO-OP
DePuy Synthes Orthopaedics - Rotation 1 Projects
Spring 2014 - January 6th to May 6th
REFLECTION
FROM THIS ROTATION, I HAVE UNDOUBTEDLY GAINED TREMENDOUS INSIGHT INTO ENGINEERING APPLICATIONS NOT ONLY IN QUALITY ASPECTS, BUT ALSO WITH REGARDS TO ORTHOPEDICS AND THE BIOMEDICAL ENGINEERING FIELD AS A WHOLE. QUALITY ENGINEERING HAS TAUGHT ME THE REALITY OF ENGINEERING IN THE CORPORATE WORLD, WHERE THE SAFETY, COMPLIANCE, AND CONTROL MUST BE PRIORITIZED IN PRODUCTION OF IMPLANTS DESTINED TO INTERACT, OFTENTIMES DIRECTLY, WITH THE HUMAN BODY. WORKING IN MANUFACTURING GAVE ME AN OUTLOOK INTO THE BREADTH OF THE ORTHOPEDIC WORLD, LEARNING THE DIFFERENT PRODUCTS, THEIR APPLICATIONS, THE MANUFACTURING PROCESS, LOGISTICS, FINANCIAL IMPACTS, AND EVEN EXPOSURE TO RESEARCH AND DEVELOPMENT AND THE CLINICAL TRIAL PROCESS. THIS EXPERIENCE, JUST THE FIRST SESSION, GAVE ME A MUCH BETTER INSIGHT INTO THE ORTHOPAEDIC INDUSTRY THAN I EVER IMAGINED IT WOULD.
PROJECTS